In the world of heavy machinery and construction, safety is paramount. Occupational Safety and Health Administration (OSHA) plays a crucial role in setting regulations to ensure safety standards are met in workplaces, particularly where heavy machinery is involved, such as aerial lifts. In this blog post, we’ll explore the depths of OSHA’s Aerial Lift Regulations and the general regulations for Diesel Mechanic Service Shops. Not only would you want to understand the rules, but also understand the best practices to maintain a safe and healthy work environment with the use of equipment like aerial lifts.
Key Takeaways
-
OSHA’s aerial lift regulations, which include §1926.453, are crucial for ensuring safe operation. They require operator training, adherence to ANSI standards, like A92.2–1969, daily functional checks, and proper stabilization and positioning to prevent workplace accidents.
-
Employers in diesel mechanic service shops are required by OSHA to provide a safe working environment, which includes implementing hazard communication programs, providing adequate safety equipment like PPE, and ensuring proper tool usage and maintenance to prevent injuries.
-
Adherence to OSHA regulations is not only legally mandatory but also a professional obligation for employers. Non-compliance may lead to severe fines, with penalties up to $15,000 per serious violation, emphasizing the importance of emergency preparedness and comprehensive employee safety training.
Understanding OSHA's Aerial Lift Regulations
In the realm of occupational safety, it’s imperative to grasp OSHA’s regulations, including 1926 subpart l. OSHA’s aerial lift regulations, particularly §1926.453, are designed to ensure the safe operation of aerial lifts, such as scissor lifts, by enforcing proper stabilization, positioning, and access. These comprehensive safety guidelines cover a wide range of aerial lifts including:
-
Extensible boom platforms
-
Aerial ladders
-
Articulating boom platforms
-
Vertical towers
-
Any combination of these devices.
To ensure the safe usage of these devices, OSHA mandates that operators undergo training and certification in occupational safety. The aim is to equip workers with the knowledge and skills necessary for operating the machinery safely and effectively.
One of the primary safety requirements for aerial lifts, as established by OSHA, is that they adhere to the American National Standards for ‘Vehicle Mounted Elevating and Rotating Work Platforms,’ ANSI A92.2–1969. This standard, approved by the Director of the Federal Register, provides comprehensive guidelines to ensure the safety of aerial lifts, including the maximum intended load.
Beyond adhering to these standards, lifts must also undergo daily control checks to verify their functionality. Additionally, when in the lower traveling position, aerial ladders must be secured. These measures ensure that all scaffold components, including ladder jack scaffold, needle beam scaffold, and self contained adjustable scaffold, are in compliance with OSHA regulations and contribute to a safer working environment.
While this is a brief overview of OSHA’s regulations for aerial lifts, we will further delve into the best practices for stabilization, positioning, and proper access and egress.
Stabilization and Positioning Best Practices
Stabilizing a scissor lift might seem like a simple task, but it’s a process that requires meticulous attention. According to OSHA regulations and industry expertise, the optimal methods for stabilizing a scissor lift involve situating it in unobstructed areas with ample space. It should be placed on a stable, even surface, with the presence of safety mechanisms verified.
The importance of proper positioning can’t be overstated. Placement on a firm and level surface, away from potential hazards, significantly contributes to the stability of a scissor lift. OSHA’s safety guidelines emphasize the importance of:
-
Avoiding electrocution hazards near power lines
-
Implementing traffic control to separate the lift from other activities
-
Ensuring worker safety through tie-offs or guardrails
Beyond mere rule-following, the key to proper stabilization and positioning lies in avoiding common blunders. Using the lift in windy conditions, moving it with the scaffold platform raised and someone on it, and not properly assessing work areas for hazards before operation can all lead to accidents. Therefore, maintaining awareness of surrounding hazards and adhering to safety protocols are crucial in preventing accidents related to scaffold systems, including those involving dismantling supported scaffolds, working with form scaffold, utilizing pump jack scaffold, handling roof bracket scaffolds, as well as using suspension scaffolds, window jack scaffold, and scaffold planks.
Ensuring Proper Access and Egress
Ensuring safe access and egress is vital in scissor lift operation. According to OSHA and ANSI regulations, an operator must be authorized in writing by the manufacturer before exiting a boom platform at height. This applies to all mobile elevating work platforms, including scissor lifts.
Potential hazards that could affect access and egress in scissor lifts include:
-
Slips, trips, and falls
-
Ground conditions such as uneven surfaces and inclines
-
Falling objects
-
Manual handling
Employers must address these existing and predictable hazards to ensure worker safety.
To facilitate proper access and egress in scissor lifts, fall protection equipment, including a full-body harness and a suitable lanyard, is utilized. These measures, when properly implemented, can significantly reduce the risk of accidents and ensure the safe operation of scissor lifts.
General OSHA Regulations for Diesel Mechanic Service Shops
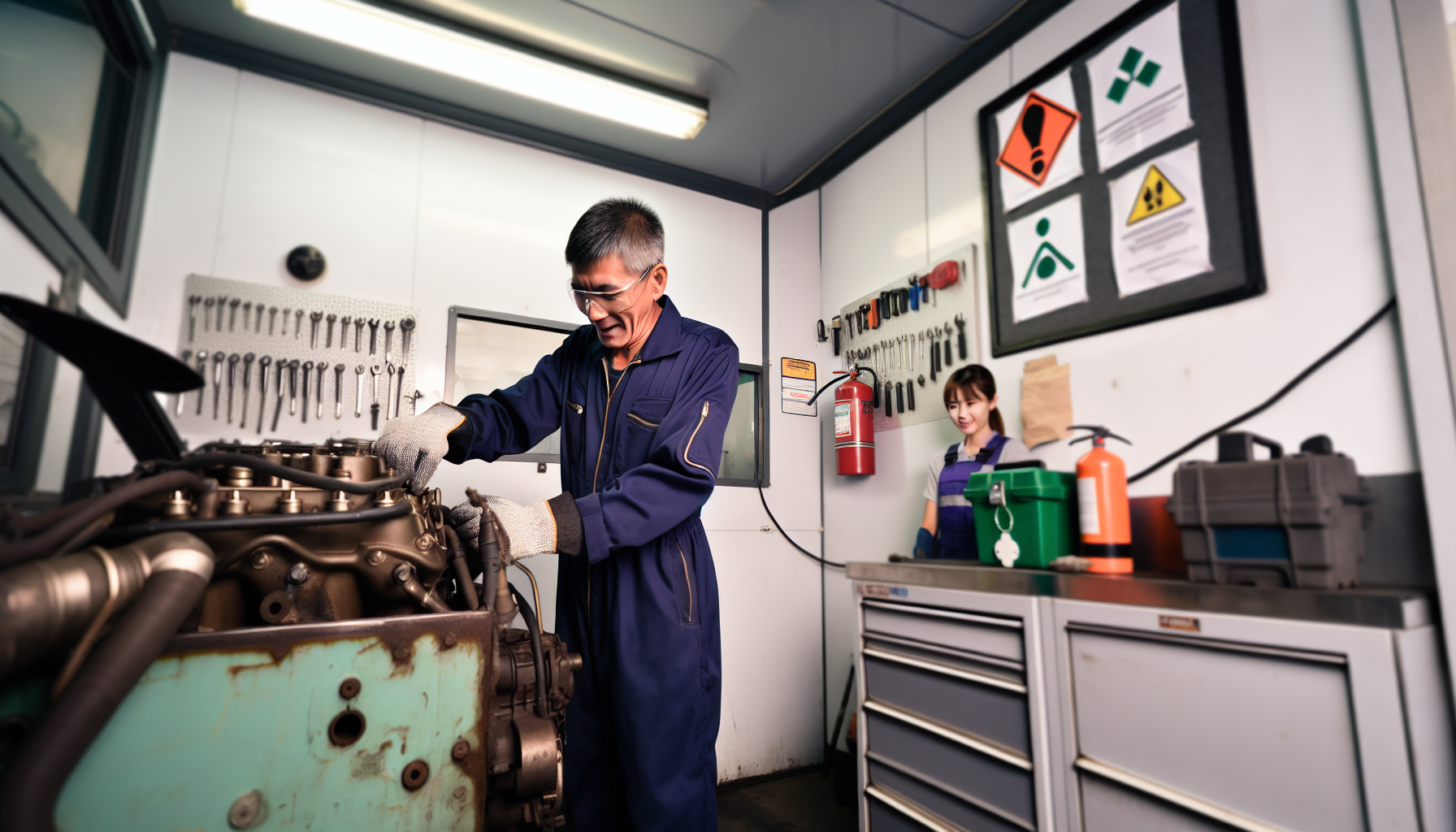
Moving from aerial lifts to the ground level, another area where safety regulations are paramount is diesel mechanic service shops. General OSHA regulations cover a range of safety aspects, including:
-
Hazard communication
-
Safety equipment
-
Tool usage
-
Shop layout
Hazard communication is a critical aspect of safety in diesel mechanic service shops. OSHA regulations mandate employers to implement a written hazard communication program. This encompasses:
-
Comprehensive training on the hazards associated with chemicals used in the facility
-
Ensuring proper labeling of chemical containers
-
Making the written program accessible to employees upon request.
Another focal area of OSHA regulations for diesel mechanic service shops is safety equipment. To ensure compliance, shops are required to provide their employees with appropriate safety and protective equipment. This includes personal protective equipment (PPE) like safety glasses, gloves, and respiratory protection, as well as equipment for working on scaffold platforms.
OSHA regulations also cover tool usage in diesel mechanic service shops. Service shops must provide suitable safety and protective equipment for tool usage. Specific guidelines can be found in the OSHA standards for the auto repair industry.
The layout of a shop plays a vital role in safety, and OSHA standards mandate certain requirements for hazard communication, the utilization of personal protective equipment (PPE), and fire safety. More comprehensive details on these standards can be accessed through the OSHA website.
Non-compliance with OSHA regulations can lead to severe penalties. Fines of up to $12,934 per violation may be levied for failure to comply with these regulations. As we examine this further, we’ll dissect specific regulations and their significance to safety standards in diesel mechanic service shops.
Right to Know Standard
The Right to Know Standard, alternatively known as the Hazard Communication Standard (HCS), is a fundamental regulation of OSHA. Its objective is to grant employees the right to be informed about hazardous chemicals present in the workplace and guarantee access to information regarding their potential risks and proper handling.
Hazardous substances and chemicals covered by this standard encompass health hazards like carcinogens, reproductive toxins, and physical hazards such as flammable substances and explosives. These are classified as hazardous according to OSHA’s Hazard Communication Standard and are accompanied by safety data sheets (SDSs).
Employers have a legal obligation to adhere to OSHA’s Hazard Communication Standard by maintaining safe work environments, providing information about hazardous chemicals, and guaranteeing the safety of their employees’ work conditions. The mandatory training for employees should cover hazard communication, utilization of safety data sheets (SDS), recognition and labeling of hazardous chemicals, and more.
Provision of Adequate Safety Equipment
As mandated by OSHA regulations, diesel mechanic service shops must equip their employees with sufficient safety gear. This includes:
-
Personal Protective Equipment (PPE) like safety glasses, gloves, and protective clothing
-
Fire safety equipment
-
Hazard communication equipment
-
Machine guarding
-
Respiratory protection equipment
The ‘adequacy’ of safety equipment is determined by its effectiveness in safeguarding against workplace hazards. OSHA does not establish a precise definition of ‘adequate’ for this equipment. Rather, employers are required to evaluate these hazards and supply the appropriate safety equipment accordingly.
Failure to comply with this regulation can attract significant fines. OSHA has the authority to levy fines of up to $15,000 per violation for the absence of adequate safety equipment in diesel mechanic service shops. These penalties underscore the gravity of non-compliance and emphasize the significance of adhering to regulations.
Tool Usage and Maintenance
Correct tool usage and maintenance play a pivotal role in ensuring safety in a diesel mechanic service shop. Recommended best practices for maintaining tools include:
-
Investing in high-quality tools specifically designed for diesel mechanics
-
Conducting regular inspection and cleaning
-
Ensuring proper lubrication of moving parts
-
Storing tools in a clean and organized manner
-
Using tools for their intended purpose and avoiding misuse
-
Replacing damaged or worn-out tools promptly
Following these practices will help keep your tools in good condition and ensure safe and efficient work in the shop, especially when working with solid sawn wood planks.
The frequency of tool inspection as per OSHA regulations depends on the type of tool and its usage. Regular inspections help in maintaining the longevity of the tools and prevent accidents due to malfunction or wear and tear.
Incorrect tool usage can lead to accidents, causing:
-
burns
-
punctures
-
cuts
-
electrocution
Therefore, proper safety measures and adherence to best practices are crucial to prevent these incidents.
Shop Layout and Safety Standards
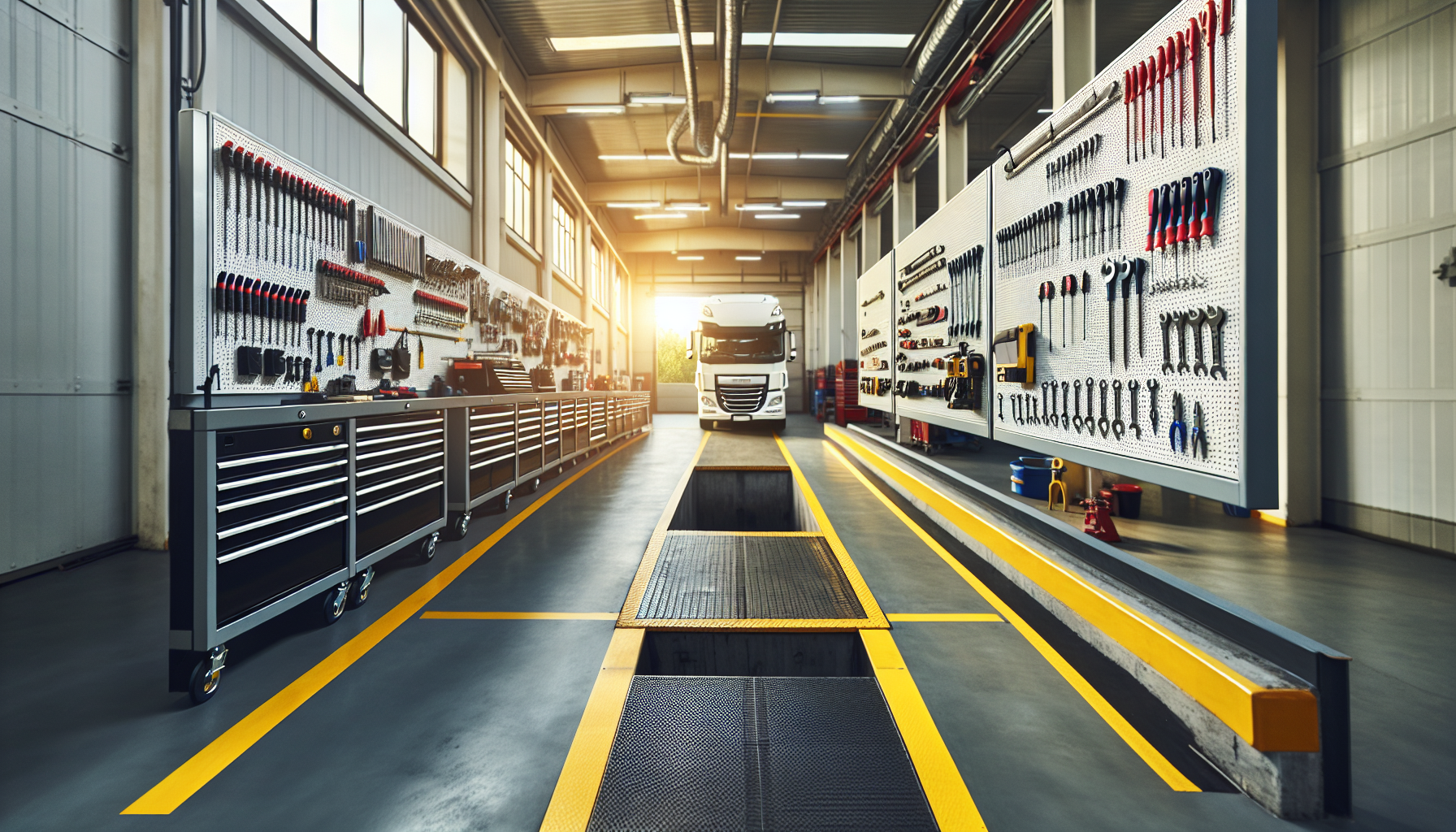
The arrangement of a diesel mechanic service shop significantly contributes to upholding safety standards. A well-planned workshop layout contributes to hazard prevention by minimizing exposure to potential hazards, safeguarding workers from moving machinery, and enhancing overall safety.
When creating a workshop layout, it is essential to:
-
Clearly delineate distinct areas
-
Provide adequate space for movement
-
Ensure accessibility of safety equipment
-
Incorporate proper ventilation and lighting
-
Designate hazardous areas.
OSHA standards mandate certain requirements for hazard communication, the utilization of personal protective equipment (PPE), and fire safety in the layout of diesel mechanic service shops. Compliance with these standards ensures a safe and efficient work environment.
Legal and Professional Responsibilities
Maintaining a safe work environment entails specific legal and professional responsibilities for employers. According to OSHA regulations, employers are legally obligated to:
-
Ensure a work environment devoid of serious recognized hazards
-
Comply with OSHA standards
-
Guarantee the use of safe tools and well-maintained equipment
-
Minimize risks in aerial lift operations.
These responsibilities extend to providing comprehensive training for employees. Employers are legally obligated to provide comprehensive training for employees, including specific safety training for operating aerial lifts, and to facilitate access to professional training resources to ensure compliance with OSHA regulations.
Beyond being a legal obligation, ensuring a safe work environment is an intrinsic professional duty for service shop employers. This encompasses equipment maintenance, fostering a respectful and inclusive workplace, and compliance with labor laws and OSHA regulations.
Non-compliance with OSHA regulations can lead to severe penalties. Fines of up to $15,000 per serious violation may be levied, emphasizing the importance of adherence to these regulations.
Emergency Preparedness and Response
Despite strict adherence to safety regulations, emergencies can arise. Hence, having an emergency preparedness and response plan is of utmost importance. Emergency, as defined by OSHA in the realm of workplace safety, is a situation that poses a threat to workers, customers, or the public, disrupts or halts operations, or results in physical or environmental harm.
An effective workplace emergency preparedness plan should incorporate specific vital steps. These include:
-
Formulating an emergency action plan that delineates employee responses to various emergencies.
-
Maintaining a written emergency action plan accessible to employees in the workplace.
-
Regularly conducting employee training on the emergency action plan.
The essential components of an emergency action plan as outlined by OSHA include the presence of a written document detailing the plan and its availability to employees for review. It’s crucial to have a plan in place, but also to make sure it’s communicated effectively to all employees.
While emergencies can strike without warning, their impact can be mitigated with thorough planning and training. Adhering to OSHA guidelines for emergency preparedness can ensure a swifter, more effective response when an emergency does occur.
Summary
Throughout this blog post, we’ve taken an in-depth look at OSHA regulations for aerial lifts and diesel mechanic service shops, along with the best practices for maintaining safety in these areas. From understanding the importance of proper stabilization and positioning to the provision of adequate safety equipment and ensuring proper access and egress, it’s clear that a commitment to safety is crucial in these industries.
As we conclude, it’s important to remember that safety isn’t just about compliance with regulations. It’s about creating a culture where safety is prioritized and every worker feels protected. After all, a safe workplace is a productive workplace.
Frequently Asked Questions
What is the OSHA standard for scissor lifts?
OSHA standard for scissor lifts requires employees to attach a lanyard to their safety harness, securely anchored to the lift, and for scissor lifts to have guardrails in place to prevent falls. It's important for workers to follow these regulations to ensure their safety while operating scissor lifts.
What safety devices are required on a scissor lift?
Scissor lifts are required to have guardrails to prevent workers from falling, along with other safety devices such as a safety trip bar, overload warning device, maintenance support bar, and safety dust cover. It is important to ensure all necessary safety devices are present and in good working condition to protect workers.
What are the safety procedures for a scissor lift?
To ensure safety while using a scissor lift, always keep work within easy reach, avoid leaning away from the lift, and never stand on, step up on, or step over the guardrail components. Additionally, always keep both feet firmly planted on the platform and never climb up the scissor lift mechanism to reach the platform basket.
Do you need a lanyard in a scissor lift?
Yes, according to OSHA guidelines, workers in a scissor lift must wear a body belt and attach a lanyard to the boom or basket for safety. It's important to also check the manufacturer's instructions.